

But compared to some of the old school methods of making your own boards, it’s relatively straightforward.
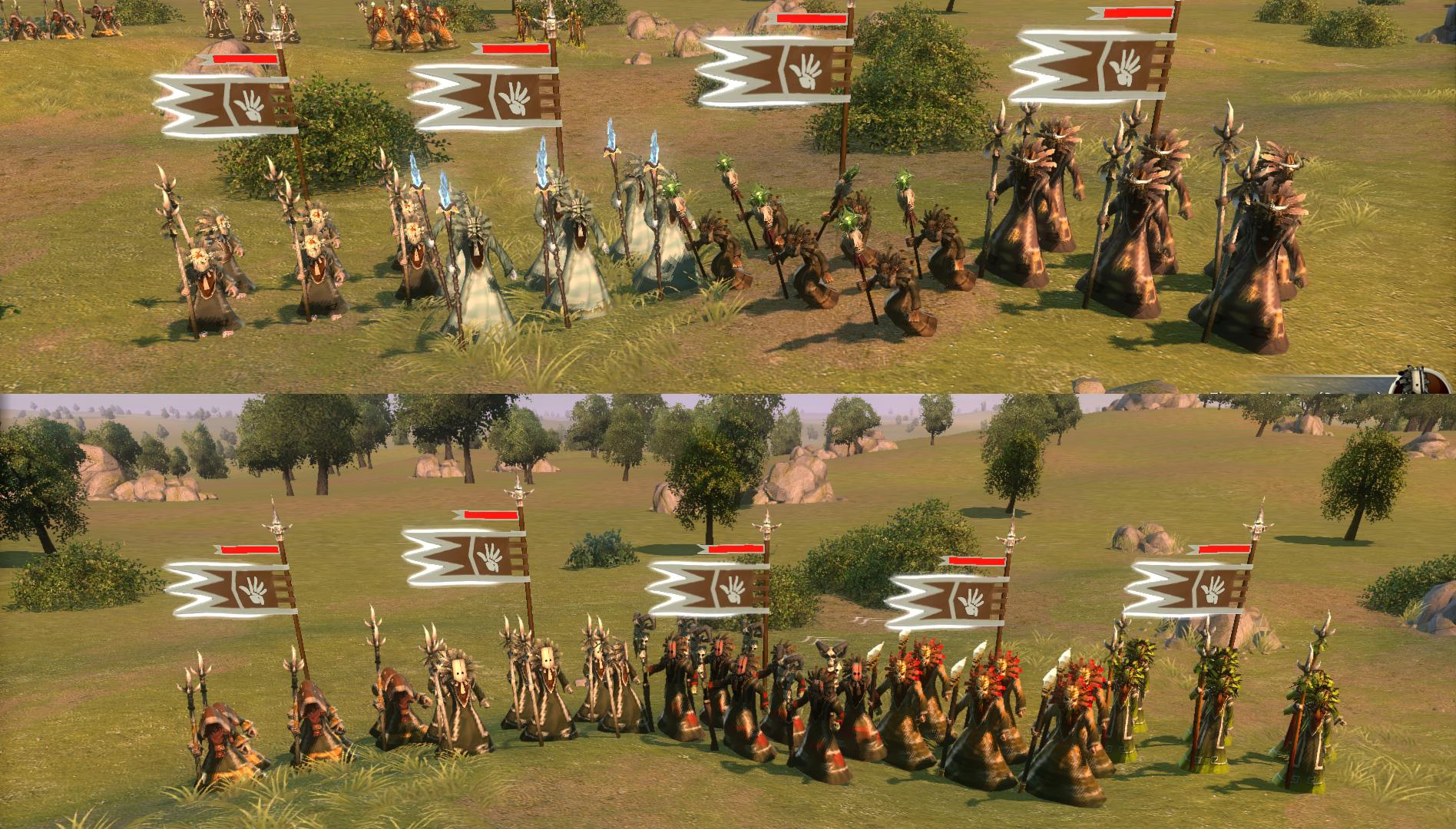
You’ll still need to chemically etch the board, and if you’re using through-hole components, manually drill your holes. Afterwards, isopropyl alcohol can be used to wash away the unexposed mask, leaving behind your PCB design. This is then placed over a copper clad board that has been coated with soldermask, and a UV light source is used to expose it. has done an excellent job of documenting the process through a step-by-step guide posted on Hackaday.io, and has also put together a video you can see after the break.īut if you’re looking for the short version, the process involves taking a 2D DXF from your PCB design software, converting it into three dimensions, and printing it out. Small “bridges” need to be manually added to hold the stencil together.
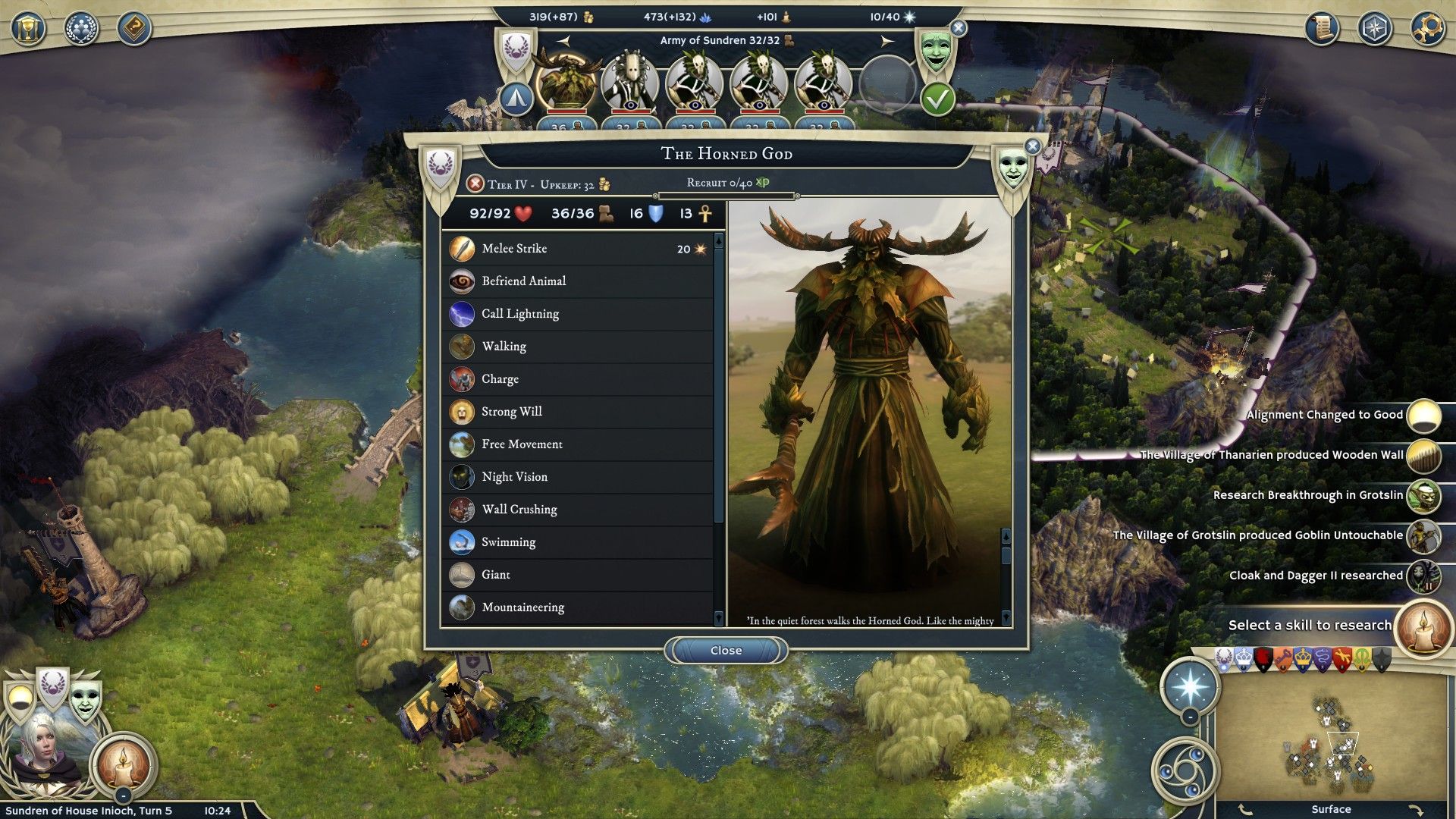
It may not be an ideal choice for densely packed boards with fine-pitch components, but could definitely see it being useful for many prototypes. This unique approach uses a desktop fused deposition modeling (FDM) 3D printer throughout all of its phases, from creating a stencil based on the exported board design, to warming the UV soldermask to accelerate the curing process. If you find yourself in such a situation, this new method of DIY PCB production detailed by might be just what you need. But even if getting your boards professionally made is cheaper and easier than it ever has been before, at-home production still can’t be beat when you absolutely must have a usable board before the end of the day. With the low-cost PCB fabrication services available to hackers and makers these days, we’ll admit that making your own boards at home doesn’t hold quite the appeal that it did in the past.
